Diecast Parts Top 5 Features & Benefits
Diecast parts are a cornerstone of modern manufacturing, playing a vital role in various industries. They offer a unique combination of strength, precision, and cost-effectiveness, making them a preferred choice for engineers and designers worldwide. This article explores the top 5 features and benefits of diecast parts, shedding light on their significance and why they are essential in a multitude of applications. Understanding these advantages will help you appreciate the value and versatility of diecast components, especially when considering options from suppliers like those available through Diecast Parts Co Za.
What are Diecast Parts
Diecast parts are created through a manufacturing process known as die casting, where molten metal is forced under high pressure into reusable steel molds, called dies. This process allows for the production of intricate and complex parts with high precision and excellent surface finish. The materials typically used in die casting include zinc, aluminum, magnesium, copper, and lead-based alloys. Die casting is particularly well-suited for high-volume production runs, making it a cost-effective solution for various industries. This process has become an important technology in many areas, from automotive to consumer electronics. It is a crucial element for manufacturing.
The Diecasting Process
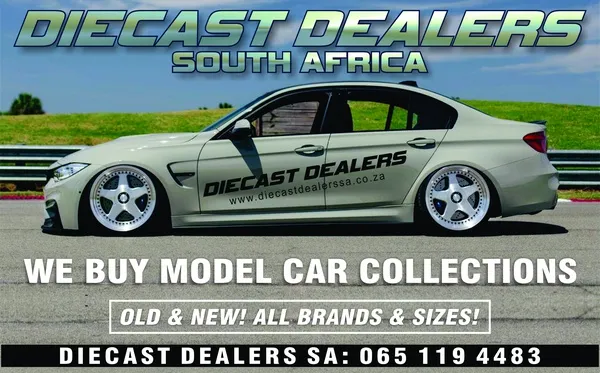
The die casting process involves several key steps. First, the metal alloy is melted and held at a specific temperature. The molten metal is then injected into the die cavity under high pressure. Once the metal has solidified, the die is opened, and the part is ejected. The part may then undergo secondary operations such as trimming, machining, or surface finishing. Careful control over each stage of the process is crucial to ensure the quality and consistency of the finished parts. The precision of this process ensures that diecast parts are highly reliable. The final parts will also have great detail.
Benefits of Diecast Parts
The benefits of using diecast parts are numerous, making them a popular choice across many sectors. These advantages contribute to their widespread use and are key in determining manufacturing choices. The following features highlight the value that diecast parts bring to various applications.
High Production Rates
Die casting is known for its high production rates, making it ideal for mass production. The ability to quickly produce large quantities of parts is a significant advantage, helping to reduce production costs and meet high demand. The speed of the process is a key factor in industries that require a continuous supply of components. This characteristic makes die casting a very efficient process, which is good for manufacturers. High production rates allow for streamlined manufacturing processes.
Complex Shapes and Designs
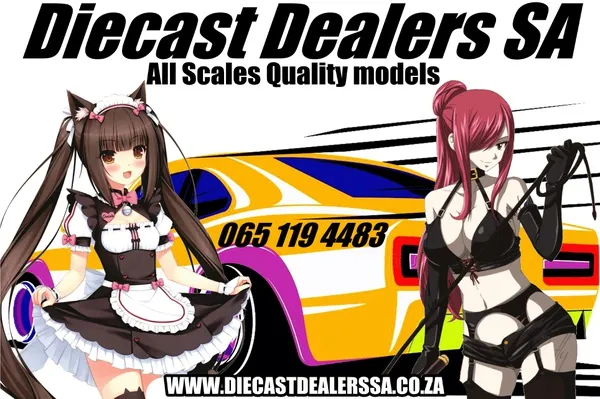
Die casting allows for the creation of intricate and complex part designs that would be difficult or impossible to achieve with other manufacturing methods. This capability allows engineers and designers to create parts with complex geometries, integrated features, and fine details. The flexibility in design opens up new possibilities for product innovation and functionality. This process allows for almost limitless design options, making it perfect for challenging design constraints.
Dimensional Accuracy and Stability
Die casting produces parts with tight tolerances and excellent dimensional accuracy. This precision is crucial for applications where parts must fit together perfectly and function reliably. The process ensures that parts maintain their shape and dimensions over time, even under stress. This reliability is important for ensuring product quality. The precision of die casting reduces the risk of defects and improves overall product performance.
Material Versatility
A wide range of materials can be used in die casting, including aluminum, zinc, magnesium, and various alloys. This versatility allows manufacturers to choose the material that best suits the specific requirements of the part. Different materials offer different properties, such as strength, corrosion resistance, and thermal conductivity. The flexibility in material selection makes die casting a versatile process that can be adapted to various applications. The selection of the right material is a critical step in ensuring the part meets its performance requirements.
Excellent Surface Finish
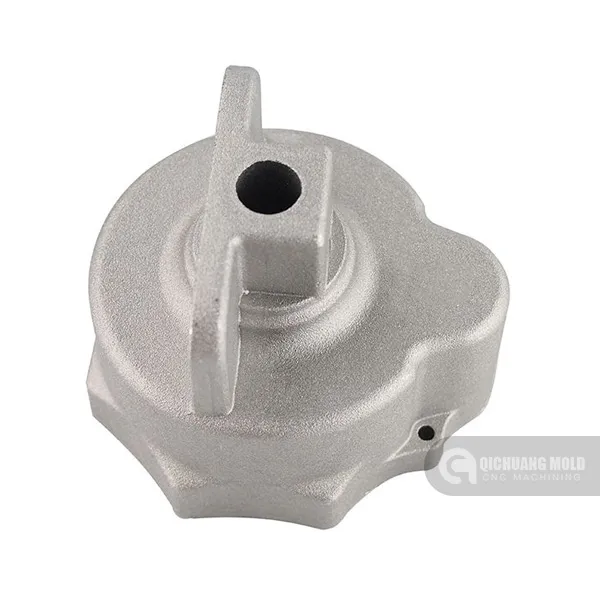
Die casting provides parts with an excellent surface finish, often eliminating the need for additional finishing operations. This smooth surface enhances the appearance of the part and can improve its performance. The high-quality surface finish can also be beneficial for applications that require coatings or plating. The smooth surface finish also contributes to the longevity of the part. The quality of the surface finish is a key factor in the overall appearance and functionality of the part.
Applications of Diecast Parts
Diecast parts are used in a wide variety of industries, demonstrating their versatility and importance. From the automotive industry to consumer electronics, the applications are vast and varied. Their ability to meet specific requirements has contributed to their widespread acceptance.
Automotive Industry
The automotive industry is a major consumer of diecast parts. These components are used in engines, transmissions, and body components. The precision, strength, and dimensional accuracy of diecast parts make them ideal for demanding automotive applications. The use of diecast parts contributes to the performance, safety, and durability of vehicles. Diecast parts, such as engine blocks and transmission housings, are essential components of the vehicles we drive daily.
Electronics
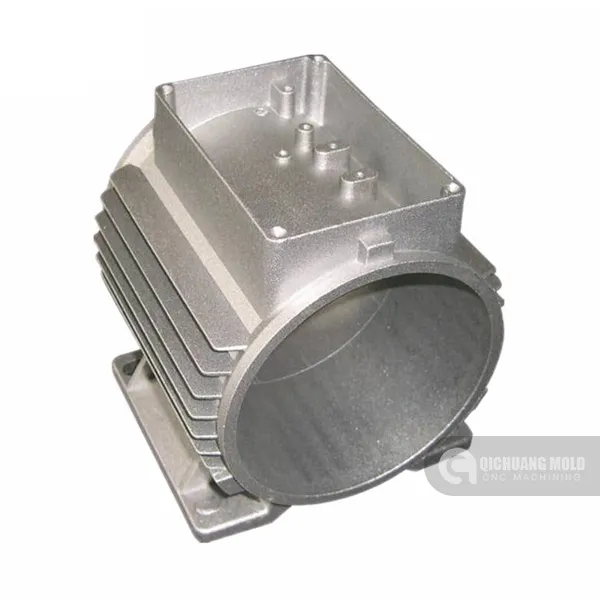
Diecast parts are also essential in the electronics industry. They are used in housings, connectors, and heat sinks. The ability to produce intricate designs and excellent thermal conductivity makes die casting suitable for electronic components. The use of diecast parts in electronics helps to improve the performance and reliability of devices. These parts help to keep electronic devices cool and functional, helping the device’s lifespan.
Hardware and Tools
Hardware and tools often incorporate diecast parts. These components are used in various tools and hardware items, such as power tools and hand tools. The strength, durability, and precision of diecast parts make them ideal for these applications. The use of diecast parts in hardware and tools contributes to their reliability and performance. Diecast parts in these tools also help to ensure longevity.
How to Choose Diecast Parts
Choosing the right diecast parts involves careful consideration of several factors to ensure the components meet specific needs. From material selection to design considerations, the selection process must align with the product’s application. These points help guide the selection process.
Material Selection
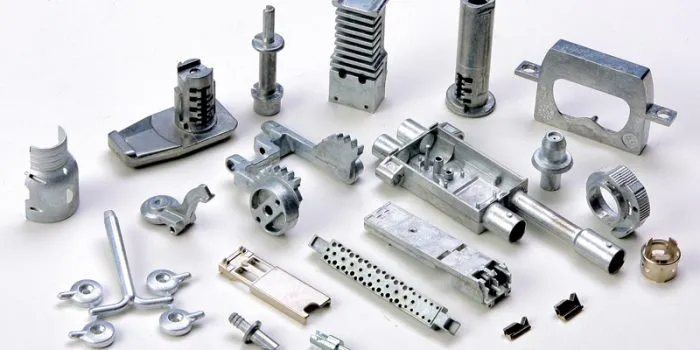
The selection of the correct material is crucial. The material should provide the necessary properties for the intended use. Aluminum, zinc, and magnesium are common choices, each offering different characteristics. Consider factors such as strength, corrosion resistance, and thermal conductivity. Proper material selection ensures the component’s reliability and longevity. Understanding the properties of each material is a key part of the selection process.
Design Considerations
Design considerations play a crucial role in optimizing the performance and manufacturability of diecast parts. Design the part to minimize sharp corners and ensure draft angles to aid in ejection from the die. Consider the complexity of the design and its impact on production costs. Work closely with die casting suppliers to optimize the design for the process. The design phase is a vital step, so consider all aspects of the product.
Surface Finishing Options
Surface finishing options can enhance the appearance, performance, and durability of diecast parts. Consider the type of finish needed to meet the requirements of the application. Options include painting, plating, and powder coating. Surface finishes can provide corrosion protection, improve wear resistance, and enhance the aesthetic appeal. The correct finish also impacts longevity and performance.
Diecast Parts Co Za
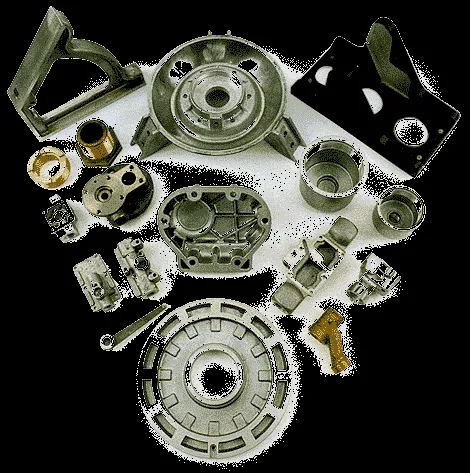
When sourcing diecast parts, consider the benefits of working with a supplier like Diecast Parts Co Za, especially if you are located in South Africa. Local suppliers offer many advantages that can improve your project outcomes and streamline the procurement process. By choosing a local supplier, businesses can experience improved service and better results.
Why Choose Diecast Parts Co Za
Choosing Diecast Parts Co Za offers several advantages. Local suppliers typically have a better understanding of the regional market and its specific needs. They may also provide more competitive pricing due to reduced transportation costs. Local suppliers are usually more accessible and can provide faster lead times. These factors can contribute to streamlined project management and cost savings. Choosing local suppliers helps ensure efficiency in the supply chain.
Benefits of Local Suppliers
Working with local suppliers offers several key benefits. These suppliers provide the ability to quickly address concerns, offering quicker responses. Local suppliers are often able to offer customized solutions tailored to specific project requirements. The ability to communicate directly with the supplier can lead to better project outcomes. Local suppliers also usually have a thorough understanding of local regulations and industry standards.
Customer Service and Support
Excellent customer service and support are critical when selecting a diecast parts supplier. Ensure the supplier provides responsive communication and is committed to meeting your needs. Look for suppliers that provide technical assistance, design support, and post-sales service. Good customer service helps to build a long-term partnership and ensures a smooth experience. The support offered by a supplier is a crucial factor in the project’s success. Good communication from the supplier ensures positive results.
Conclusion
Diecast parts offer numerous benefits, making them a vital component in a wide range of industries. From their high production rates and design flexibility to their dimensional accuracy and material versatility, diecast parts provide superior performance and cost-effectiveness. Understanding these features and benefits will help you make informed decisions when selecting diecast parts for your projects. Consider partnering with reputable suppliers like Diecast Parts Co Za to ensure you receive high-quality parts and excellent customer service.