Diecast Aluminum Specifications Overview
Diecast aluminum is a versatile and widely used material in various industries due to its excellent properties and cost-effectiveness. Understanding the specifications of diecast aluminum is crucial for engineers, designers, and manufacturers to ensure the final product meets the required performance criteria. This guide provides a comprehensive overview of the essential specifications, helping you choose the best diecast aluminum for your specific needs. From material grades and mechanical properties to design considerations and applications, we’ll cover everything you need to know to make informed decisions.
Material Grades and Alloys
The selection of the appropriate aluminum alloy is the first step in diecast aluminum specifications. Different alloys offer varying combinations of properties, making some more suitable for specific applications than others. Choosing the right alloy ensures the final product’s strength, corrosion resistance, and overall performance. Material grades are typically designated by industry standards such as those from the Aluminum Association or similar organizations. These grades define the chemical composition and mechanical properties of the aluminum, providing a baseline for comparison and selection.
Common Aluminum Alloys in Die Casting
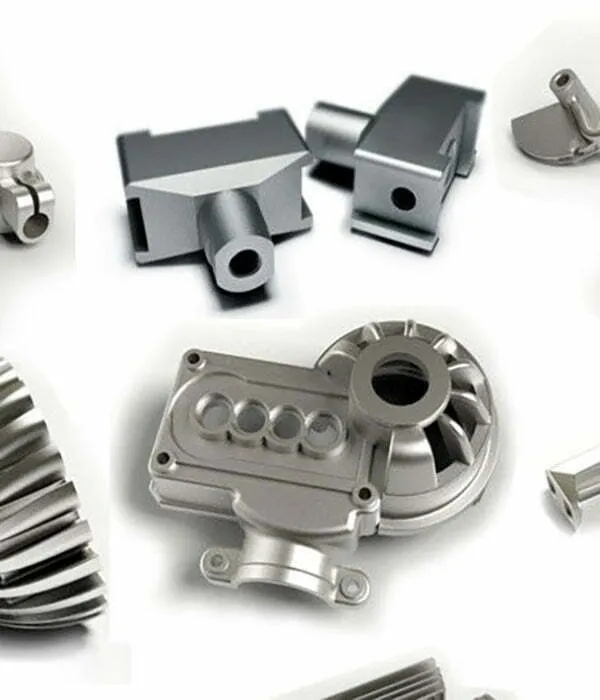
Several aluminum alloys are commonly used in die casting, each with unique characteristics. Alloy A380 is one of the most popular due to its excellent castability, mechanical properties, and cost-effectiveness. A380 is suitable for various applications, including automotive components and consumer electronics housings. Alloy A360 offers superior corrosion resistance, making it ideal for products exposed to harsh environments, like marine applications. Alloy ADC12, a Japanese standard, is also widely used due to its good balance of properties and castability. The choice of alloy depends on the specific requirements of the application, including strength, corrosion resistance, and cost considerations.
Mechanical Properties of Diecast Aluminum
Mechanical properties define how an aluminum part behaves under different forces. Understanding these properties is essential for predicting the performance and lifespan of the diecast component. Key mechanical properties include tensile strength, yield strength, elongation, and hardness. These properties are directly influenced by the chosen alloy, casting process, and any subsequent heat treatments. Analyzing these parameters allows engineers to ensure the diecast part can withstand the stresses and loads it will experience in its operating environment.
Tensile Strength
Tensile strength measures the maximum stress a material can withstand before it begins to neck or break under tension. A higher tensile strength indicates a stronger material more resistant to pulling forces. Diecast aluminum parts often require specific tensile strength values to meet performance requirements. For instance, components in the automotive industry might require higher tensile strength to endure the stresses of driving and impact. Ensuring the tensile strength meets the specified requirements is crucial for the part’s structural integrity.
Yield Strength
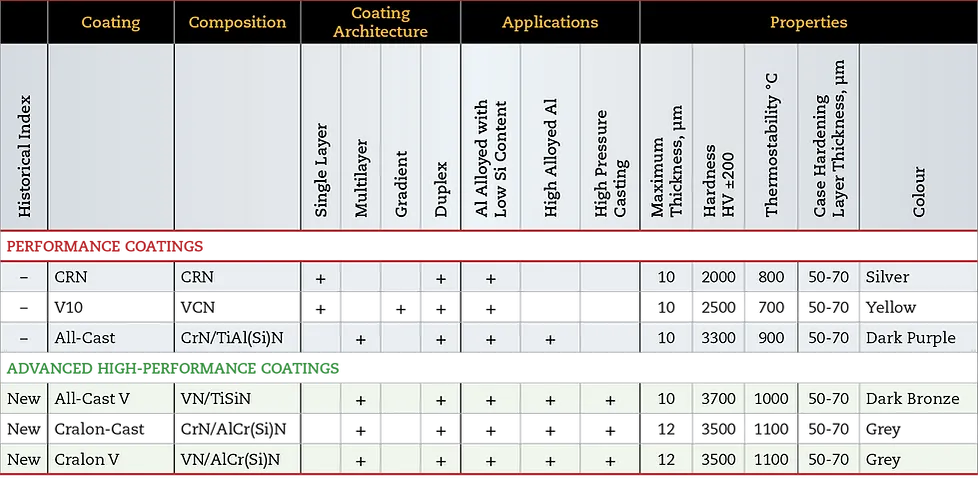
Yield strength is the stress level at which a material begins to deform permanently. Below this point, the material will return to its original shape once the stress is removed. Above this point, it undergoes plastic deformation. Yield strength is critical for applications where the component is subjected to constant or repeated stress. A higher yield strength means the material can withstand greater loads without permanent deformation, providing increased reliability and longevity. Selecting an alloy with an appropriate yield strength is essential for the component’s functional performance.
Elongation
Elongation measures the material’s ability to stretch or deform before fracturing, expressed as a percentage. Higher elongation indicates a more ductile material, which can absorb more energy before breaking. This property is important for components that may experience impact or sudden loads. Ductile materials are generally more resistant to cracking under stress. Diecast aluminum alloys offer a range of elongation values, allowing engineers to select the optimal alloy based on the application’s requirements.
Dimensional Accuracy and Tolerances
Dimensional accuracy is essential for ensuring that diecast aluminum parts fit correctly with other components and function as intended. Tolerances define the acceptable variation in dimensions. Close tolerances are critical for parts that require precise alignment or mating surfaces. The die casting process can produce parts with relatively tight tolerances compared to other manufacturing processes. However, achieving high dimensional accuracy requires careful control over the casting process, including factors such as die design, alloy selection, and process parameters. The specification of tolerances directly impacts the cost and manufacturability of the diecast part.
Factors Affecting Dimensional Accuracy
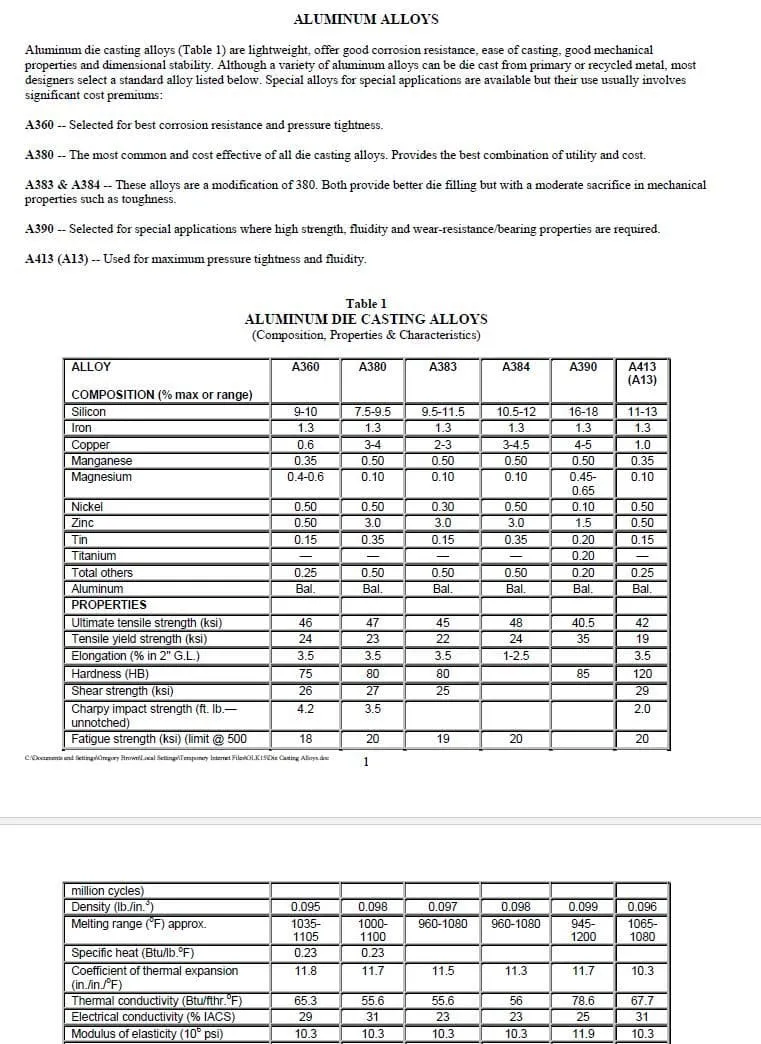
Several factors influence the dimensional accuracy of diecast aluminum parts. Die design plays a crucial role, including the precision of the die cavity and the use of appropriate draft angles. Alloy selection affects dimensional stability during cooling. Process parameters like injection pressure, die temperature, and cooling rates significantly influence part dimensions. Post-processing operations, such as machining, can further refine the dimensions and improve accuracy. Proper control over these factors is essential for achieving the desired dimensional accuracy and ensuring the part meets its functional requirements.
Surface Finish and Treatments
Surface finish and treatments enhance the appearance, corrosion resistance, and functionality of diecast aluminum parts. The surface finish can range from a raw as-cast finish to highly polished surfaces. Surface treatments involve applying coatings or modifying the surface to improve properties. Surface finish is specified based on the desired aesthetic and functional requirements, such as the need for paint adhesion or corrosion protection. The choice of treatment directly affects the cost, durability, and overall performance of the part.
Common Surface Treatments
Several surface treatments are commonly applied to diecast aluminum parts. Powder coating provides a durable and aesthetically pleasing finish, offering excellent corrosion resistance. Anodizing creates a protective oxide layer, improving corrosion resistance and wear resistance while enhancing the part’s appearance. Painting provides a decorative finish and protects against environmental factors. Plating can enhance the surface properties, such as electrical conductivity or wear resistance. The selection of the surface treatment depends on the application, operating environment, and desired appearance of the final product.
Design Considerations for Diecast Aluminum
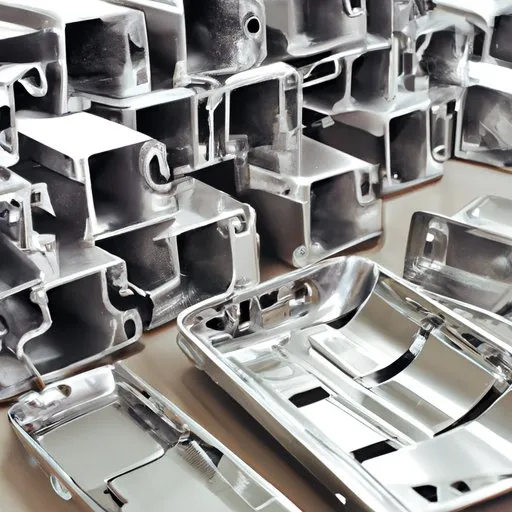
Designing for die casting requires specific considerations to optimize manufacturability and cost-effectiveness. Proper design can minimize defects, improve dimensional accuracy, and reduce production costs. Key design elements include wall thickness, draft angles, ribs, bosses, gates, and runners. Considering these elements early in the design process can significantly impact the success of the diecast aluminum part. Collaboration between designers and die casters is crucial for achieving the best results.
Wall Thickness and Draft Angles
Wall thickness is an important design consideration affecting the part’s strength, weight, and cooling characteristics. Uniform wall thickness is generally preferred to avoid stress concentrations and ensure consistent cooling. Draft angles are slight tapers on the side walls of the part, which allow the part to be easily ejected from the die. Insufficient draft angles can lead to part damage or difficulty in ejection. Optimizing wall thickness and draft angles is essential for efficient and high-quality die casting.
Ribs and Bosses
Ribs and bosses are design features that increase the rigidity and strength of a diecast aluminum part. Ribs provide structural support without increasing overall wall thickness, while bosses provide mounting points for fasteners or other components. Proper design of ribs and bosses includes considerations for their height, width, and placement. These design elements can enhance the performance and functionality of the part. Careful planning is needed to ensure they do not interfere with the casting process or cause other issues, such as stress concentrations.
Gates and Runners
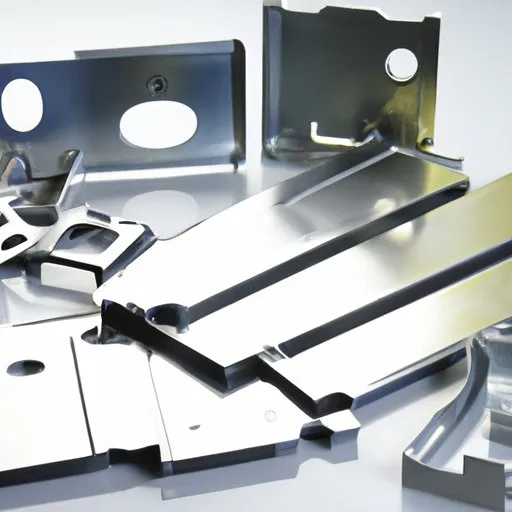
Gates and runners are integral to the die casting process, providing the path for molten aluminum to flow into the die cavity. The design of gates and runners influences the filling of the die cavity, the formation of defects, and the overall quality of the part. Proper gate placement is crucial to ensure uniform filling and minimize porosity. Runner design optimizes the flow of molten metal to reduce turbulence and improve casting efficiency. Careful consideration of gates and runners is vital for producing high-quality diecast aluminum parts.
Applications of Diecast Aluminum
Diecast aluminum is utilized in diverse applications due to its versatility, strength, and cost-effectiveness. Its lightweight properties, coupled with its ability to be cast into complex shapes, make it an ideal choice across various industries. The specific requirements of each application dictate the appropriate alloy selection, surface treatment, and design considerations. Its ability to withstand high temperatures and environmental conditions makes it a preferred choice for many demanding applications. The applications range widely, demonstrating the versatility and adaptability of diecast aluminum.
Automotive Industry
The automotive industry is a significant consumer of diecast aluminum parts. These parts are used in engines, transmissions, chassis components, and body parts. Diecast aluminum offers a high strength-to-weight ratio, contributing to improved fuel efficiency and vehicle performance. Common automotive applications include engine blocks, cylinder heads, transmission housings, and suspension components. As the automotive industry increasingly focuses on lightweighting and performance, the demand for diecast aluminum parts continues to rise. Innovations in die casting are enabling the production of even more complex and efficient automotive components.
Consumer Electronics
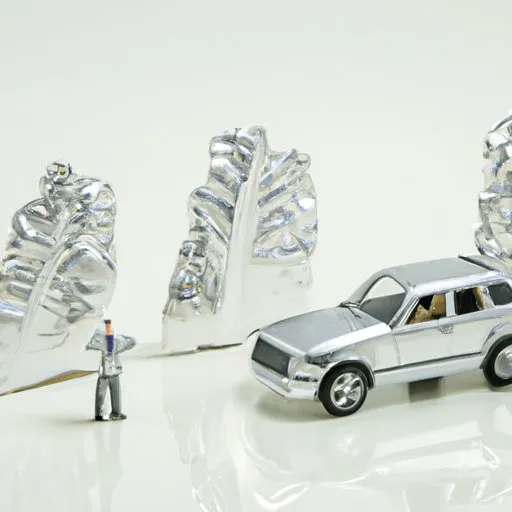
Diecast aluminum is widely used in consumer electronics for housings, heat sinks, and other components. Its excellent thermal conductivity makes it ideal for dissipating heat from electronic components. The ability to cast complex shapes and integrate features, such as mounting points and vents, further enhances its appeal. Common applications include laptop housings, smartphone frames, and electronic device enclosures. The aesthetic versatility and design flexibility of diecast aluminum also make it suitable for various consumer electronics products. Its use contributes to product durability and the sleek appearance desired by consumers.
Industrial Machinery
Industrial machinery utilizes diecast aluminum for various components, including housings, gearboxes, and structural parts. The strength, durability, and corrosion resistance of diecast aluminum make it suitable for these demanding applications. The ability to withstand harsh operating conditions and high loads is a significant advantage. Common industrial applications include pump housings, motor housings, and machine frames. The material’s long-term reliability and resistance to wear and tear contribute to reduced maintenance costs and increased operational efficiency.
How to Select the Right Specifications
Selecting the right diecast aluminum specifications requires careful consideration of several factors, including application requirements, cost considerations, and quality control. The choice of alloy, mechanical properties, dimensional tolerances, and surface treatments must align with the performance demands of the final product. A thorough understanding of these factors ensures that the diecast aluminum part meets all necessary requirements and performs reliably in its intended application. Consulting with experienced die casting professionals is often beneficial.
Application Requirements
Understanding the specific requirements of the application is the first step in selecting the right diecast aluminum specifications. This includes the operating environment, the loads and stresses the part will experience, and any specific performance criteria. Factors to consider are temperature range, exposure to corrosive substances, and any need for electrical conductivity. The application requirements drive the selection of the alloy, mechanical properties, and surface treatments. Comprehensive knowledge of these aspects ensures the part is designed to meet performance demands.
Cost Considerations
Cost is often a significant factor in the selection of diecast aluminum specifications. The cost of the alloy, the complexity of the die casting process, and the required surface treatments all contribute to the overall cost. While choosing the lowest-cost option may seem appealing, it is crucial to balance cost with performance and reliability. Optimizing the design, selecting the appropriate alloy, and considering alternative manufacturing processes can help minimize costs without compromising quality. Careful analysis and value engineering are essential to find the optimal balance between cost and performance.
Quality Control and Testing
Quality control and testing are essential to ensure that diecast aluminum parts meet the specified requirements. These processes verify that the parts meet dimensional tolerances, mechanical properties, and surface finish specifications. Various testing methods are used, including dimensional inspections, tensile testing, and corrosion resistance testing. These tests provide assurance that the parts are manufactured correctly and will perform reliably in their intended application. Implementing a comprehensive quality control plan throughout the die casting process is critical for delivering high-quality products.
In conclusion, understanding diecast aluminum specifications is crucial for achieving optimal results in various manufacturing applications. From material selection and mechanical properties to design considerations and quality control, each aspect plays a vital role in the performance and reliability of the final product. By carefully considering the factors discussed in this guide, engineers and designers can make informed decisions and select the best diecast aluminum specifications to meet their specific needs. The versatility, strength, and cost-effectiveness of diecast aluminum make it a valuable material in many industries.